PROJECT EXAMPLES
Kelken Construction Systems manufactures & distributes high quality anchoring products and accessories that help improve jobsite productivity. Below are some real world jobsite applications.
RAIL PROJECTS
SILVERLINE DULLES CORRIDOR METRO RAIL PROJECT
This project jobsite is the new commuter rail line and switching yard running from Washington DC to Dulles International Airport. The jobsite contractor, VIAS USA Contracting of Sterling Virginia is using Ultrabond Epoxy Adhesive for the installation of the track fixators into concrete. ULTRABOND1 is manufactured by Adhesives Technology Corporation and distributed in the Northeast by Kelken.
FORMER DOW CHEMICAL PLANT RETROFIT JOB
Keligrout™ high strength polyester resin anchoring material was used at this Piscataway New Jersey jobsite. KINKISHARYO International, LLC is turning the former DOW Chemical plant into a railcar repair, remodel and upgrade facility. Kelken anchoring products are being used in the securing of the new rail lines.
The new plant can now retrofit old rail cars into modern functional transportation by easily moving the cars through various work stations. Work on the job was performed by Tracks Unlimited of Mountianside, New Jersey.
LONG ISLAND RAILROAD
Kelken Construction Systems supplied the anchoring material to the contractor, Kiewit Infrastructure Group for the retrofit of rails on the Long Island Railroad. Rehab of the direct fixation for the track consisted of removing the old fixators redrilling new holes and replacing everything under the track. High strength Ultrabond 1 Epoxy is being used to anchor the rails, providing a fast and secure process of direct rail fixation.
ROAD & BRIDGE PROJECTS
I-495 BRIDGE PROJECT WILMINGTON, DE
The Interstate Highway 495 bridge over the Christina River in Wilmington Delaware was closed because supporting columns were visibly tilting. Delaware transportation officials said the bridge would probably be closed until at least Labor Day and could be shut down much longer if the tilting section needs to be completely replaced. The bridge typically carries about 90,000 vehicles a day on an eleven mile bypass around Wilmington DE. Traffic is being shifted onto already congested Interstate 95 through downtown. Engineers suspect that a massive mound of dirt dumped next to the bridge caused the movement of underground soils, which resulted in the cracking of concrete footers supporting the columns and damage to the steel pilings driven into bedrock.
A repair plan was formulated which involved a temporary stabilization that would allow traffic to once again move across the bridge. The columns under the west roadway were the ones tilting and the contractor J.D. Eckman of Atglen, PA wanted to make sure the superstructure as well as the involved columns did not move any farther before and during the construction of new columns under the substructure. The plan was to take 3″ diameter steel dywidag bars and attach them to the substructure from the east pier to the tilting west pier. These were placed on both sides of the columns and remained in place during new column construction and the jacking of the bridge. Kelken’s Keligrout 101-P high strength anchoring material was used to secure the dywidag bars in place during the emergency repair.
After temporary repairs were completed the bridge reopend to traffic after thorough testing. DOT workers used sensors to monitor roadway stability while six heavy Delaware DOT trucks loaded with wet sand were driven onto the repaired spans and then stopped mid-way. The repairs passed with flying colors and traffic once again flows on 495 over the bridge.
CONCRETE BARRIER ANCHORING NEW HAVEN, CT
When working in a high speed high traffic area, like I-95, taking the proper safety precautions to protect roadside workers is vitally important. Those concrete safety barriers that we frequently see lining the sides of major highways often serve as the first and last line of defense for contractors. To be effective those barriers need to be held securely in place, an easy enough job to do with standard concrete anchoring materials. The problem is that most concrete anchoring products are designed to be permanent and the barriers are a temporary safety precaution that need to be moved frequently as the workers move on to new sections of highway. Uprooting and moving concrete barriers that are held in place with a permanent concrete anchoring system is a very time consuming, labor intensive process. This makes a versatile high strength removable anchoring system for the barriers an absolute must for highway construction projects. Enter Kelken with their polyester resin anchoring material Keligrout and their custom sized removable Kelianchors.
In late 2009 Florida based construction company Walsh Group was awarded the contract to repair the Pearl Harbor Memorial Bridge in New Haven, CT. Heavy construction began in February and is expected to last through 2012. The concrete deck on both the north and south lanes needs to be replaced, and repairs are needed on the superstructure and bearings of the entire bridge. Much of the work is being completed at night, and in segments, reaffirming the need for an anchoring system that would securely hold the safety barriers in place, yet allow them to be moved to the next work zone protection area with minimal removal time. Kelken’s chemical anchoring system provided just the solution they were looking for.
For securing the barriers anchors were drilled into 3” of asphalt until they hit concrete. They were then drilled an additional 7” into the deck. The holes were filled with Keligrout and the anchors coated with Kelislip, a Teflon solution allowing the anchors to be turned out of the Keligrout when needed. Using this system the barriers were able to provide work zone protection while the deck on the northbound side was being reconstructed. When this portion of the project was complete the anchors were simply spun out of their holes, thanks to the Keligrout, and reused on the next work zone protection area.
MARINE & WATER PROJECTS
PORT NEWARK – ELIZABETH MARINE TERMINAL PROJECT
Port Newark – Elizabeth Marine Terminal is a major component of the Port of New York and New Jersey. Located on the Newark Bay it serves as the principal container ship facility for goods entering and leaving New York-Newark metropolitan area, and the northeastern quadrant of North America. On August 15, 1962, the Port Authority opened the world’s first container port, Elizabeth-Port Authority Marine Terminal. Elizabeth became known as America’s Container Capital. Maher Terminals, LLC operates the portion of the terminal currently under retrofit for foul weather safety systems.
It is the largest container port in the eastern United States and the third largest in the country. Container goods typically arrive on container ships through the Narrows and the Kill Van Kull before entering Newark Bay, a shallow body of water which is dredged to accommodate the larger ships. The port facility consists of two main dredged slips and multiple loading cranes. Metal containers are stacked in large arrays visible from the New Jersey Turnpike before being loaded onto rail cars and trucks.
Simpson & Brown of Cranford, NJ is providing the Engineering and Maintenance services on the job. They have been hired to test and replace when necessary the anchor hold down cable attach points on the pier that secures the large container cranes waterside in case of extreme weather conditions. The anchors are 2″ X 50″ High Strength Hurricane Tie-Downs, pictured in photos.
KELKEN Construction Systems Keligrout™ is being used in the retrofitting of the hurricane tie downs. This is a reinstall of large anchors that were originally cast in years past and have since failed. Each anchor’s design load is 149,000 lbs tensile strength and the total per hurricane attachment is 849,000 lbs. The original anchors were core drilled out, then the holes were scarified with a carbide tipped Kelken provided tool. The holes were then cleaned and the anchors installed with Keligrout or if the hole was too large in diameter Keligrit was used to prevent adhesive shrinking.
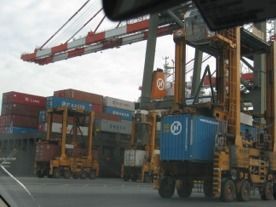
Port Elizabeth NJ Cargo Terminal
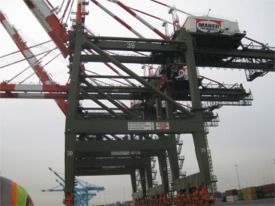
Kelken Keligrout is used for anchoring
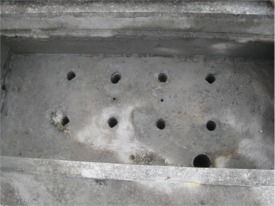
Concrete base is prepared for anchors
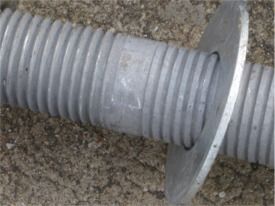
2″x50″ Hurricane Anchor
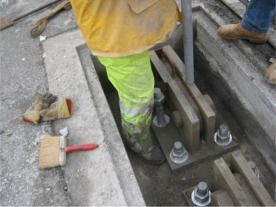
Anchor hold down cable attach point
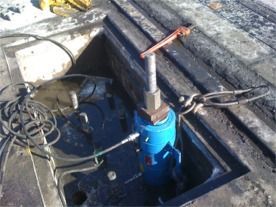
100 ton center hole ram jack loading crane tie down anchors
BOUNDBROOK, NJ – FLOOD GATE
The Raritan River flows adjacent to the town of Boundbrook, NJ and has a long history of flooding the town. The Metro Railroads elevated road bed provides a natural dike that helps to protect the town from flooding. There are portions of the railroad bed with tunnels that connect except Main St out of town to join Rt 206 and I-287 thru the tunnel.
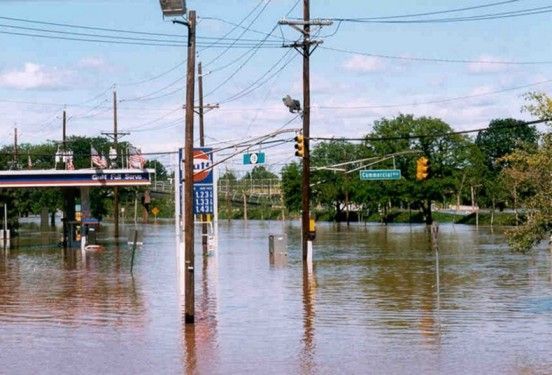
The Army Corp built 2 flood gates to protect the town at the tunnel locations and the moving flood wall tracks cross the Main St. Plates were installed to move traffic over the tracks smoothly and the traffic has loosened the plate’s anchors. Re-drilling and re-anchoring with Keligrout and removable anchors with Kelislip applied that were torqued down after the adhesive cure fixed the problem.
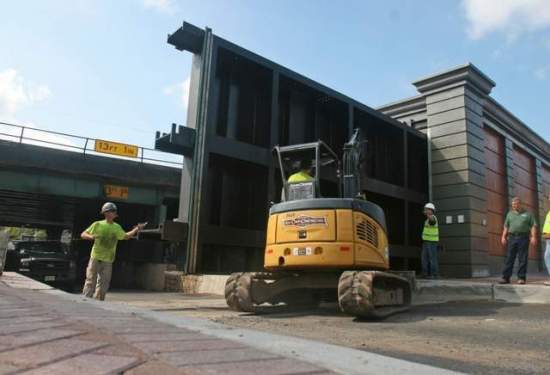
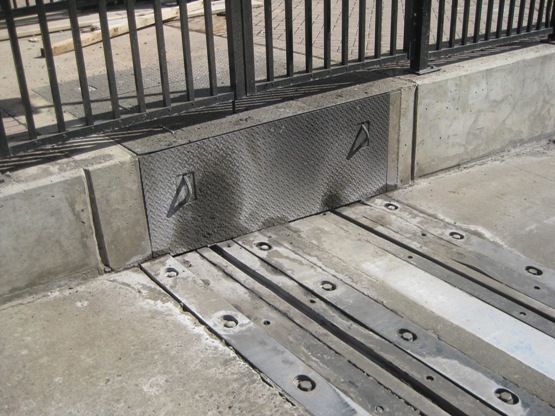
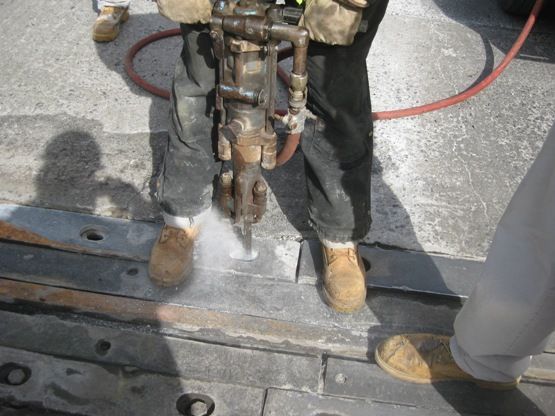
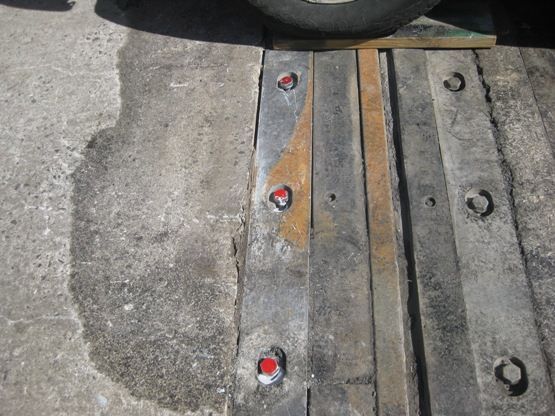
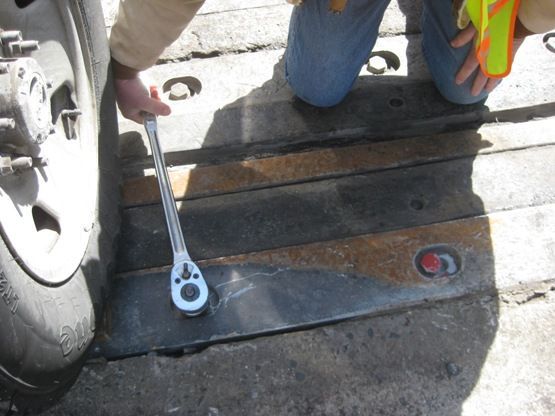
SAYREVILLE WASTE WATER TREATMENT PLANT MIDDLESEX COUNTY, NJ
This job is the retrofit of the rail system that guides a traveling bridge across the waste water holding tank. Quad Construction of Philadelphia is the installer / contractor for Gantrex Canada the manufacture of the rails and the flying bridge.
Watch our short (3 minute) job highlight video below for the product and installation details on this anchoring project. Keligrout Polyester Resin was used to secure the threaded stainless steel anchors into the concrete.
The existing rails and attachments were completely rusted out due to the highly corrosive conditions at the sediment tanks. Additionally the original hardware was only galvanized steel and the replacement hardware is all ASTM 316 stainless steel.
All the existing hardware and rails were removed from the top of the concrete tank walls, the old anchors were core drilled out of the concrete and the holes were cleaned out with compressed air. New stainless anchors installed with Keligrout from quart cans. After 24 hour cure the rail attach plates were bolted down and the rails were attached.
SITE CONSTRUCTION PROJECTS
HIGHWAY SOUND WALL CONSTRUCTION PROJECT HAUPPAUGE, NY
Kelken Construction Systems supplied Keligrout high strength polyester resin anchoring material for this highway sound wall construction project in Hauppauge New York on Long Island.
Project: The Smithtown Bypass road is not limited access like an interstate, it has many cross streets, businesses as well as traffic lights. Adjacent to portions of the roadway are exclusive upscale neighborhoods where the sound of traffic has become a problem for the residents. The installation of a 22′ tall sound wall is done to eliminate the traffic noise filtering through the area.
The sound wall construction begins with the caisson drilling form being inserted to a depth of 22 feet. A caisson reinforcing cage of steel rebar is set inside the hole for added strength before the cement is poured in. Once sufficiently cured, anchor holes in the concrete are drilled for the securing of the vertical support posts between the sound wall sections. Once drilling is completed the holes require a thorough clean out with a wire brush and then debris is blown out with compressed air. The properly prepared anchor holes are now ready to receive Keligrout and threaded anchors.
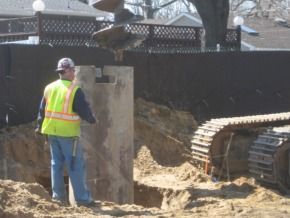
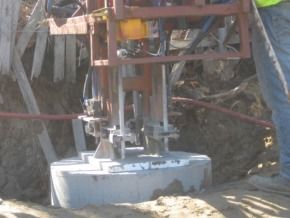
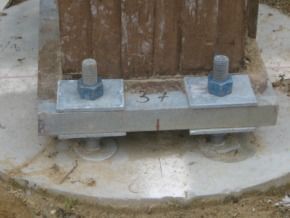
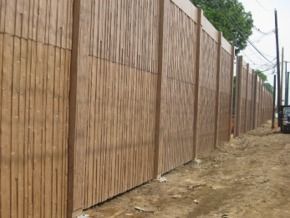
WAYNE JUNCTION STATION REMODEL & EXPANSION PHILADELPHIA, PA
Kelken products Keligrout and Kelianchors are being used for anchoring of the canopy over the new ADA compliant entrance ramp. Keligrout is a superior high strength polyester resin anchoring material with guaranteed pullout values exceeding ACI-349-85.
Wayne Junction Train Station in North Philadelphia has been a regional transportation hub since the late 1800’s. The current train station layout and structure date back to 1901. Today the station serves almost 200,000 passengers each year and yet was not fully ADA compliant, until this refurbishing project. Years of funding related problems and maintenance cutbacks had left the station in disrepair and a desperate need for updating. SEPTA has a renovation program in place that included the Wayne Junction Train and Bus Station and ADA compliance among other concerns.
The scope of work for this SEPTA project includes a new elevators and an ADA-compliant egress throughout the station. New high level platform on the inbound platform and repairs to the existing high level outbound platform. Rehabilitation of the historic site features, including the station building, Germantown Headhouse, and canopies. Restoration of passenger tunnels and stairways from Wayne Avenue, Germantown Avenue and Windrim Avenue. Improved passenger amenities including audio-visual public announcement system, signage, windscreens and benches.
TOWER PROJECTS
CELL TOWER ANCHORING RETROFIT IN NYAK NY
When cell towers were first installed they rarely had to support a maximum amount of hardware and communication equipment attached to the top and sides. The engineering and design for the towers was usually based on a moderate amount of loading required for the limited demand for space. As time goes on more and more cellular communications equipment is added to the sides and top of the structures and the original structural specs and anchor design becomes inadequate.
To keep the tower in service and increase the equipment load, it is necessary to retrofit some towers with additional structural stiffeners and anchoring to protect against a wind load failure. Additional 2″ x 9′ long concrete threaded anchors were installed into the concrete base on this anchoring retrofit job.
Kelken Chemical Anchoring products Keligrout and Keligrit were used to secure the treated steel anchors to the concrete footing. Before installing the anchors the newly drilled holes were prepared with a scarifying tool to ensure that the interior surface of the hole would provide a sufficiently rough surface for the anchors to grab.
Once the hole is blown out with compressed air it is ready for the properly prepared Keligrit which can be poured or spooned into the hole. Next the anchor is pushed to the bottom of the hole and rotated to assure total wetting. The anchor is then left undisturbed for about an hour depending on the ambient temperature at the time of installation.
Keligrout is about 50% cured after the first hour and fully cured after 24 hours. At that time the anchors on this job were pull tested to 130,000 LBS with a hydraulic jack.
Cell Tower Retrofits specialists Tower Solutions LLC, was contractor on this job. Kelken products were used on this job as anchoring material to secure the additional threaded anchors to the concrete tower base.
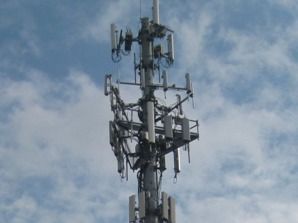
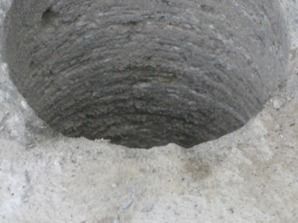
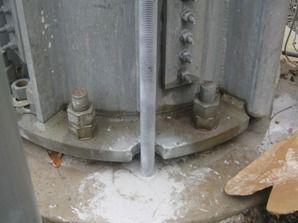
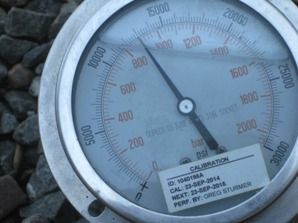
FIRE TOWER RESTORATION PIERCEFIELD, NY
Kelken anchoring products were used in the foundation retrofit of a historic fire tower on Mount Arab, located in the town of Piercefield, New York, in the northern part of the Adirondack Mountain Range. The footing were crumbling apart from old age and the anchor bolts were rusting in the harsh conditions. David Vana, a specialist in fire tower repair and restoration performed the retrofit of the tower footings.
The original footings were drilled into the Gneiss rock that makes up the mountain. Concrete footings were poured as a leveling platform for the base of the original tower legs which were anchored in the rock surface. To replace the footings and reanchor the tower without taking it completely down, it had to be done 1 leg at a time. David and his team hauled in the necessary equipment and stayed on the mountain for a couple of 4 day / night work sessions to get the job completed.
The legs had to be braced and jacked up one at a time. The old and decaying concrete footing and anchor bolts were removed from under the jacked leg. When closely inspected the old anchor bolts were nearly rusted through. The restoration proved to be a timely undertaking. After clearing the concrete and chiseling the rock to a fresh surface, new anchoring holes were drilled into the Gneiss rock. The new footing was constructed in several steps. First new stainless steel anchor bolts were set with the help of Kelken products, Keligrout polyester anchoring compound into the Gneiss rock. Next the concrete footing was framed in and reinforced with stainless steel rebar before the cement pour. On the bottom the new anchor bolts secured a mounting plate to the top of the new concrete footing. The new anchor plate bolts to the tower leg securing it on the top side of the footing. Kelken Keligrout anchoring compound and stainless steel anchors were used on this feature project.
“The Kelken products, product instructions, and their personal advice was invaluable” – David Vana
David Vana of Bloomingdale, NY performs fire tower repair, removal and reassembly across the county. He has an existing inventory of towers that have been taken down for safety and liability reasons from publicly accessible areas. Towers are occasionally purchased and then reassembembled on private land for observation and entertainment purposes.
AVIATION PROJECTS
LANDING STRIP STRIKE PLATES ANCHORED WITH KELIGROUT
The scope of work on this Kelken project includes the re-installation of tail hook strike plates. The retrofit is necessary due to the settling of the strike plates below the surface of the runway. This settling condition has allowed the aircraft tail hooks to slide over the plate and hit the concrete on each side which caused the breaking out of the area around the steel plates. See all the details in our short video presentation.
The flight deck of an aircraft carrier only has about 500 feet of runway space for landing military jets. The runways on the carriers are not nearly long enough for high speed jets to fully decelerate. To aide the landing process on the carrier flight deck, jets are equipped with a tail hook. The hook is used to achieve rapid deceleration during arrested landings aboard aircraft carriers. Pilots train to do these landing at the Naval Air Station in Meridian Mississippi.
The retrofit on the Meridian training runway began with the strike plates being removed and the old anchors core drilled out. New stainless steel anchors were installed using Keligrout polyester resin. Shims were placed under the plates to bring them level with the runway. The strike plates were bolted to the runway to complete the retrofit.
The new anchors were installed using Kelken Keligrout polyester resin to properly secure them in place. Keligrout is easily hand mixed and poured from the original container. The powder catalyst is stirred into the resin, then poured into properly prepared anchoring holes.
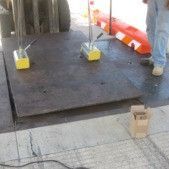
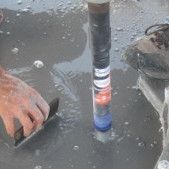
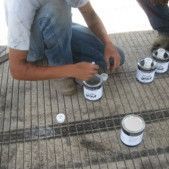